According to Assembly Mag:
Electric motors in cars are omnipresent, but they are also well hidden. In today’s late model vehicles, more than 30 motors are typically used to power a variety of applications, including ABS pumps, central locking systems, exterior mirrors, seat adjusters, window regulators and windshield wipers.
However, from a technical point of view, the most exciting aspect of electric motors are the ones used for the drivetrain in mild hybrids, full hybrids, plug-ins and purely electric cars. Even hydrogen-powered heavy-duty trucks need electric traction motors.
Electric motors are typically assembled with adhesives, because they provide impact resistance. Bonding also provides vibration-damping characteristics for noise reduction.
Externally excited synchronous motors have windings in the stator and rotor that are energized. The power density of these devices tends to be lower than that of other motor designs, while wear tends to be higher due to the use of carbon brushes. Electric vehicles with these motors, like the BMW iX3, do not require magnets.
Induction motors, another important AC drive, tend to have a lower power density and operate without magnets. These types of motors are found in the Audi e-tron and the Tesla Model S, Model Y and Model 3.
Permanent magnet motors have the highest power density. This applies especially to motors equipped with internal permanent magnets (IPM), which are found in EVs such as the Porsche Taycan. The magnets offer strong performance. However, because of the natural monopolies that surround the mining and sale of rare-earth magnets, they tend to be expensive and can be difficult to source.
Better Joining With Adhesives
As different as each of these concepts are, they share something in common: EV motors are becoming smaller and more powerful, while their efficiency continues to improve. To achieve performance goals, engineers must consider many things, including lamination design, an optimal embedding of the magnets into the lamination stack, and leaving the smallest gap possible between the magnet and coil.
Each of these things increases assembly challenges. Adhesive bonding is a great joining option, because it plays a different role depending on the motor concept. Bonding is especially important when fixing the magnets of IPMs.
For example, a progressive reduction in motor size leads to tightened manufacturing tolerances, which drives up costs. In addition, rare-earth magnets are susceptible to corrosion, which is why they receive a passivation, nickel or epoxy resin coating. It is critical that the coating not be damaged during mounting.
This coating protects the magnets from exposure to environmental influences. Other established methods of joining, such as mechanical clamping of magnets, are reaching their limits in terms of motor function and production process. Adhesive bonding, on the other hand, meets all these requirements.
Bonding is also advantageous for other motor concepts beyond joining magnets and lamination stacks. It can be used to join the shaft and rotor or the stator and housing. Adhesives can prevent fretting or contact corrosion. They are also impact-resistant, which is essential for the high dynamic forces in electric motors.
The vibration-damping characteristics of adhesives helps reduce noise and provides acoustic improvement. Their homogeneous stress distribution helps compensate for thermal stress that may be generated due to different coefficients of thermal expansion between the stator and housing.
Gap-filling properties help prevent slippage and play in the area surrounding the shaft. Often, bonding allows for lower manufacturing costs, since a high level of automation can be used.
Apart from these assembly applications, adhesives are also used for casting sensitive components in electric motors to protect them from humidity, aggressive media and mechanical stress.
Selecting the Appropriate Adhesive
Automotive engineers can choose from a wide variety of adhesive families. Given their different sizes and power densities, as well as the different environmental influences that e-motors are exposed to in the drivetrain, there is no blueprint for a universally valid design for an adhesive any more than there is for a standard production process.
Nevertheless, it is helpful to first take a look at the larger groups of adhesives together with their individual strengths and weaknesses. Then, tests should be performed on individual products, with the specific component.
In general, acrylates and polyurethanes are not suitable for most electric motors because of their moderate reliability. Anaerobic-curing metal adhesives, although used in industrial motors, are not ideal for extremely powerful electric motors for the drivetrain either. This leaves two main product groups: one-component and two-component epoxy resins.
One-Component Epoxies
One-component heat-curing epoxies feature excellent properties. They achieve good bond strength values at temperatures as high as 220 C. They are not only able to withstand peak temperatures temporarily, but they can also be used permanently at high temperatures for motors above insulation class H.
One-component heat-curing epoxy resins also exhibit high chemical resistance, good gap-filling capacity and good adhesion to nickel-plated surfaces, which is important for magnet bonding.
Heat curing with one-component epoxy is a process that takes between 20 and 40 minutes for most adhesives at typical temperatures. But, there are also newer products, including those for demanding environmental conditions that require only 10 minutes at 150 C for curing.
Induction curing is often an option for medium-sized motors or for high volumes, reducing process times by up to 90 percent and enabling accelerated curing in just one minute. In this process, the adhesives achieve the same high strength as what is achieved through standard heat curing.
Metal workpieces, which are partially or completely exposed to an electromagnetic alternating field by means of a current-carrying coil, are the precondition for induction curing. This field generates eddy currents within the material, flowing opposite of the original current and heating the material.
Induction allows very fast heating of electrically conductive components, while reducing the heating time. Energy costs for induction curing is significantly lower than those of convection ovens.
Two-Component Epoxies
For economic reasons, the larger the components are, the more manufacturers tend to choose two-component epoxies. These products are not only good for gap bridging, but they also offer excellent peel strength, equalization of tensions and good chemical resistance. In addition, they can be shipped and stored at room temperature.
Two-component epoxies cure at room temperature. The time lapse before reaching initial strength is deemed a major disadvantage for working with high-volume applications. However, two-component epoxies can be cured with heat, which accelerates the process. At a temperature of 80 C, for example, 10 minutes is sufficient to achieve adequate handling strength.
Sixty minutes gets the product to full curing. With induction curing at 100 C, the components can be fixed within one minute. After this time, a strength of 10 megapascals (MPa) is already achieved. The adhesive then achieves its full final strength at room temperature.
Depending on the adhesive, this process can take another few hours. But, this is irrelevant because the components can be processed immediately once handling strength has been achieved.
Compared to curing at higher temperatures, as is done for one-component products, these moderate conditions reduce the time needed for heating the components, leading to a lower energy demand in production.
Products for Potting Applications
In most potting applications in the EV drivetrain, which are intended to protect windings, among other things, there are often only moderate requirements. Because large quantities are needed, low-priced products are offered. For requirements beyond this, there are basically two options.
On one hand, there are dual-curing adhesives that are light-fixed and reach full strength under the influence of air, humidity or heat. They ensure fast processing while curing takes place reliably and simultaneously in shadowed areas.
For applications with extremely high requirements, there are reliable products that provide excellent resistance to aggressive media, like gear oil, or high thermal resistance with low thermal expansion. These products are available in one- and two-component variants for smaller and larger volumes, respectively. Due to their special composition, some of the products offer a coefficient of thermal expansion of up to 20 ppm/K, which is adapted to copper.
Higher Operating Temperatures
The maximum operating temperature of many electric motors is 180 C, because powerful rare-earth magnets will demagnetize at higher temperatures. That is why high-temperature resistant adhesives are in demand for use with EV motors and power electronics.
It is important to remember that adhesives are essentially plastics. With many adhesives, temperatures of 150 C or more can lead to a change in the polymer structures and a drop in performance. Often, elasticity increases above this temperature range, which is not desirable.
In recent years, the adhesives industry has been developing products that offer up to three times the strength at high temperatures than that of previous generations. For example, there are not only products that achieve strengths of up to 20 MPa on aluminum at 150 C, but also adhesives that are completely optimized for high dynamic loads in electric motors and for bonding magnets.
They achieve compression shear strengths of 20 MPa even on magnetic material (NdFeB) and at temperatures of 80 C (20 MPa corresponds to a force of 1,300 pounds on the surface of a penny).
The compounds are so thermally stable over the long term that these values can still be achieved after 10,000 hours of storage at 180 C and can be used in applications that require resistance at higher temperatures up to 220 C. This is possible through increased glass transition temperatures (Tg), which can be as high as 180 C.
As a result, the Young’s modulus does not change significantly under Tg. The adhesive achieves a very high temperature stability and only increases in flexibility above this temperature.
Light Fixation Simplifies Production
The greater the mechanical loads, the more likely it is that one-component epoxy adhesives will be used. However, for a long time, such products were only available in purely heat-curing form. As a result, fixing devices are frequently used to hold components in position during oven curing.
Today, there are adhesives with two-stage light and heat curing that simplify this process while combining high strength with very good temperature resistance. They are prefixed in about 10 seconds, depending on the chemical composition and the UV light intensity. This eliminates the need for retainers during assembly, disassembly and cleaning. In the case of electric motors, this allows buried magnets to be fixed in the rotor package without any mounting devices.
With the subsequent heat curing step required, which usually takes 20 minutes at 130 C, epoxies are able to achieve their full strength. The final strength is impressive. For aluminum, it is 60 MPa, which corresponds to a force of 3,900 pounds on the surface of a penny.
Light-fixable adhesives also exhibit high thermal and chemical resistance. In typical long-term tests of 500 hours of storage at 85 C and 85 percent relative humidity, they are able to achieve more than 75 percent of their original strength. The same holds true after 1,000 hours of storage at 200 C.
As far as temperature stability (the strength directly under the influence of temperature and not only after storage), the adhesives show very good values, but fall below the highly specialized high-temperature products. However, strengths of up to 10 MPa can also be achieved with some new light-fixable products.
Revolutionary Two-Component Adhesives
For two-component epoxies, the lengthy amount of time required to achieve initial strength was traditionally considered a disadvantage for many high-volume assembly applications. But, there are now hybrid chemistries that can be used to shorten this time a great deal and simplify production processes and logistics.
This can be achieved when light fixation is integrated into the bonding process with two-component products. Reliable final curing, including shadowed areas, is the same as for regular two-component products at room temperature. Alternatively, it can be accelerated with heat within 60 minutes at 80 C.
The first option is likely more attractive to most manufacturers, because there is an overall reduction in cycle times and throughput times, as well as energy costs for heat curing. The need for floor space is also radically reduced. Since dispensing, joining and light fixation take less than a minute, the next production step can begin much faster than the usual 15 to 90 minutes.
The light fixation strength of the products available so far is lower than that of the light-fixable one-component products. However, the components are so strongly protected against slipping after just a few seconds of irradiation that processing of the entire assembly can continue immediately.
In addition, new technology simplifies logistics because products don’t need to be transported and stored in a cooled state. A storage life of 12 months enhances production flexibility and enables the use of larger, more cost-effective containers.
These products are suitable for use in many applications, because they achieve a tensile shear strength of 28 MPa on aluminum. During the aging simulations required in the automotive industry, this value is maintained after 500 hours of storage at 85 C and 85 percent relative air humidity.
These new developments still have to prove themselves somewhat in practice, but they have great potential. This is because they combine the advantages of light curing with the strengths of two-component products. All users need is a mixing system and lamps. Ovens, energy and space on the shop floor can be saved, not to mention a great deal of time.
Additional Adhesive Properties
To increase EV traction motor performance with the same size dimensions, manufacturers are demanding electrical insulation as another property of the adhesive. This helps minimize eddy currents in electric motors, reducing heat generation and increasing performance.
In addition to high temperature resistance and electrical insulation, good thermal conductivity is also required in some cases. In some motors, heat is dissipated from the windings. Products suitable for this purpose have a thermal conductivity of about 1.5 watts per meter-Kelvin (W/mK) and an adjusted coefficient of thermal expansion in the range of 25 ppm/K.
Adhesives are sometimes equipped with integrated spacers. These spacers ensure a uniform and very thin bonding gap of 50 microns for segmented magnet stacking. This allows the use of more magnetic material and also contributes to motor efficiency.
Related Posts
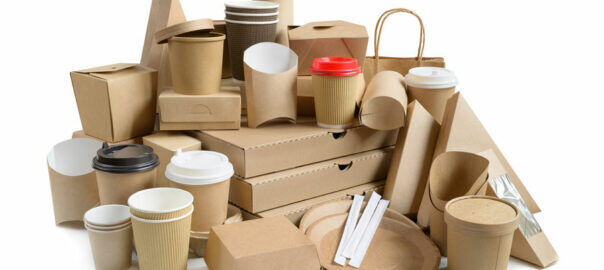
These Six Sustainable Adhesive Types Play a Big Role in Sustainable Packaging
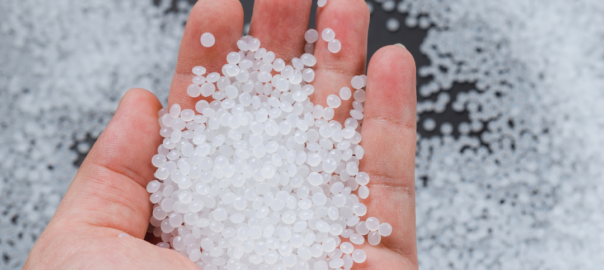